Stock Control Charts (DP IB Business Management): Revision Note
Understanding stock control charts
Stock control involves carefully planning and controlling stock flow to ensure that enough raw materials, work-in-progress and components are available to meet production demands
A stock control diagram shows how stock (inventory) moves into and out of a business over time
A stock control diagram for a small manufacturing business
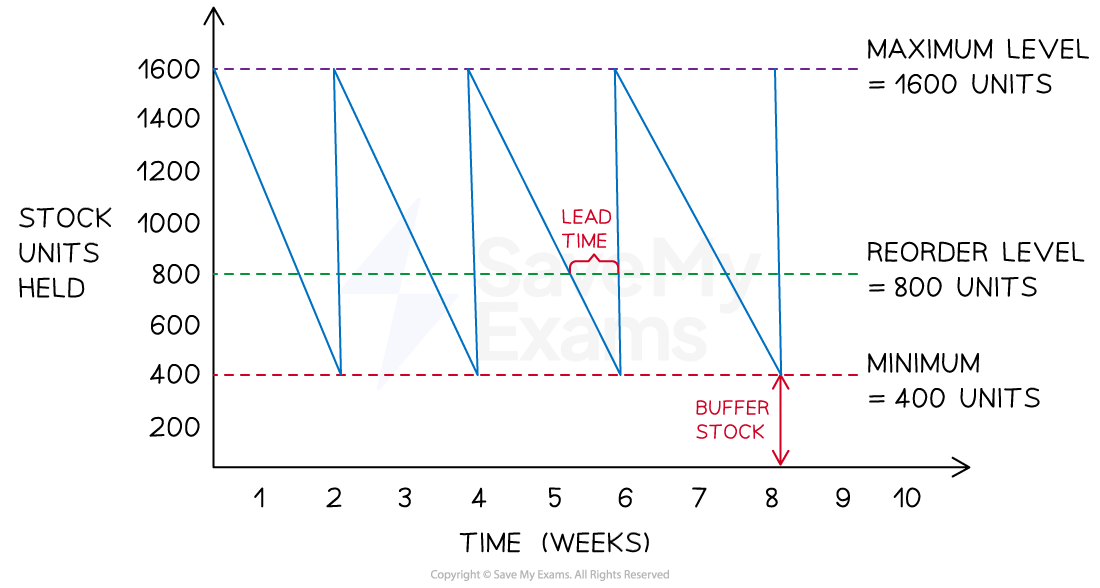
The maximum stock level is the maximum amount of stock a business is able to hold in normal circumstances (1600)
The reorder level is the level at which a business places a new order with its supplier (800)
The minimum stock level is also known as the buffer stock level and is the lowest level to which a business is willing to allow stock levels to fall (400)
The lead time is the length of time from the point of stock being ordered from the supplier to it being delivered (1 week)
The stock level line shows how stock levels change over the given time period
As stock is used up a downwards slope is plotted
When an order is delivered by a supplier the stock level line shoots upwards
Worked Example
The diagram below shows stock movements of kitchen shelving units sold by TamFix Ltd.
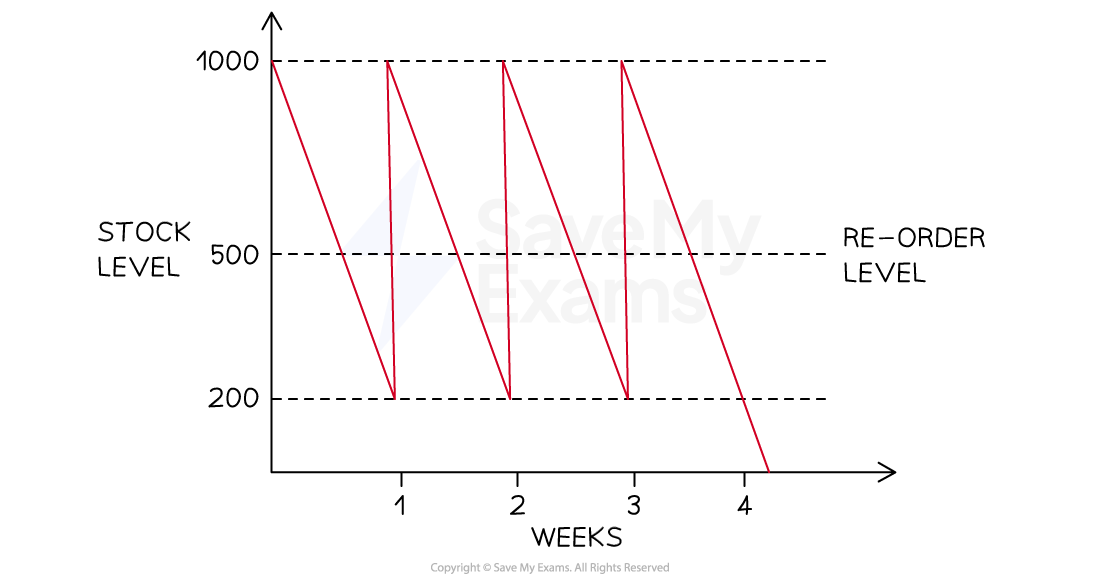
Identify the following points:
the minimum stock level
the re-order level
the re-order quantity
the lead time for kitchen shelving units
[4 marks]
Step 1 - Identify the minimum stock level
The minimum stock level is identified by the bottom-most dotted line - in this case it shows that the minimum stock level is 200 units (1)
Step 2 - Identify the reorder level
The reorder level is clearly identified on the diagram - in this case it shows that the reorder level is 500 units (1)
Step 3 - Identify the reorder quantity
The reorder quantity is the difference between the maximum stock level (shown by the topmost dotted line) and the minimum stock level
1000 units - 200 units = 800 units
The reorder quantity is therefore 800 units (1)
Step 4 - Identify the lead time for kitchen shelving units
The lead time is the difference in time between an order for stock being placed and its delivery
In this case, assuming a five-day working week, the lead time for shelving units is two days (1)
The implications of poor stock control
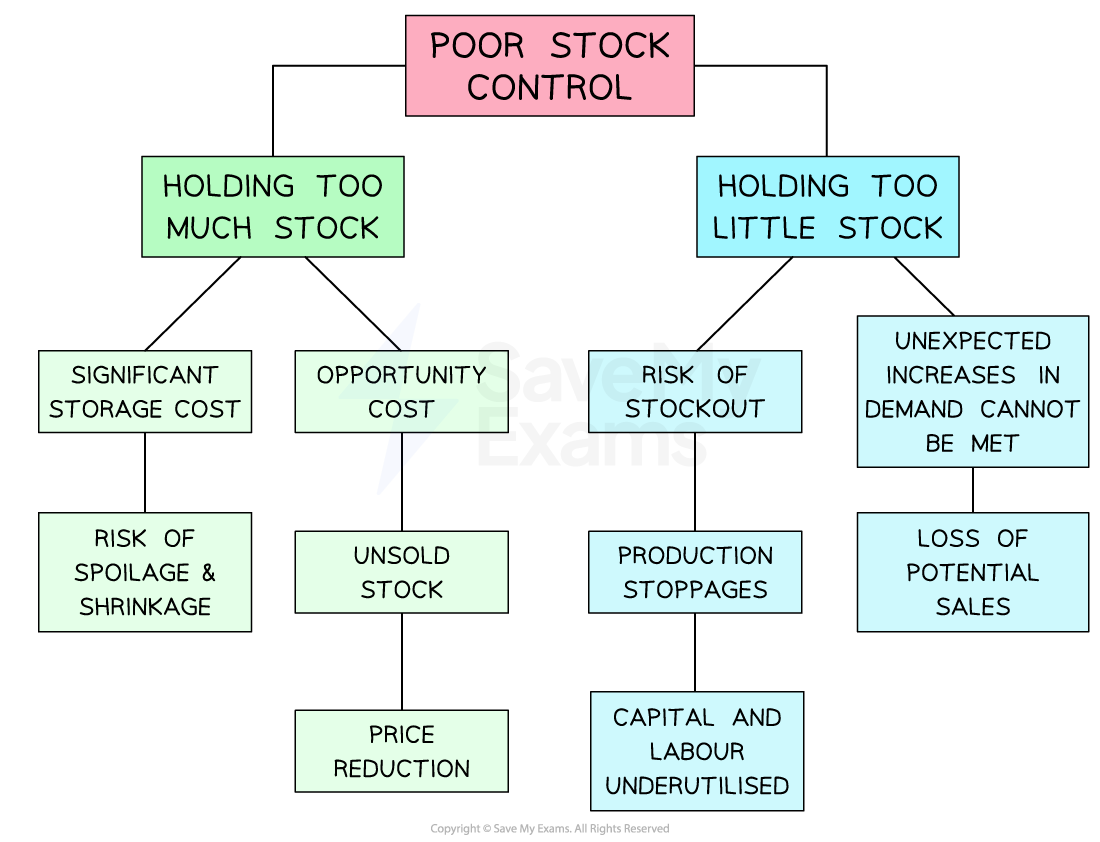
Problems may arise from holding too much stock
Storage costs (e.g. warehouse rental, security costs) will be higher than necessary
The risk of stock shrinkage or spoilage is increased
Excess stock may need to be sold at a lower price, reducing revenue
Similarly, holding too little stock is risky
A business may run out of stock, resulting in production stoppages and higher unit costs due to underused capacity
A sudden increase in demand may not be capable of being met
Examiner Tips and Tricks
Even businesses that invest heavily in complex stock control technologies can be affected by external factors that have an unanticipated impact on their ability to receive, distribute or use stock
Stock control is therefore closely linked to aspects of contingency and crisis management
You've read 0 of your 5 free revision notes this week
Unlock more, it's free!
Did this page help you?