Lean Production (DP IB Business Management) : Revision Note
Features of Lean Production
Lean production is a management philosophy that aims to maximise value while minimising waste
It focuses on maximising efficiency, improving quality and reducing costs
The main principles of lean production
Right first time approach
Aim for zero defects in output
Identify and solve problems as they arise
Prevent rather than correct errors
Flexibility
Adaptable capital equipment and physical resources
Multiskilled staff and team working
Flexible management styles
Waste Minimisation
Remove processes that do not contribute to added value
Consume as little as is necessary
Rework rather than replace
Effective supply chain management
Develop excellent relationships with suppliers
Minimal number of suppliers
Continuous improvement
Ongoing, small steps
All staff involved in improvement
The seven wastes eliminated in lean production
Waste refers to anything that prevents a business from being efficient
First developed in Japan in the 1970s, seven key types of waste are minimised in lean production
Transportation: Unnecessary movement of materials or products
Inventory: Excess raw materials, work-in-progress, or finished goods
Motion: Unnecessary movement of people or equipment
Waiting: Delays or idle time in the production process
Overproduction: Producing more than what is required by the customer
Overprocessing: Using more resources than necessary to produce a product
Defects: Products or services that do not meet customer requirements
Examiner Tips and Tricks
Reducing waste appears to be logical and, to some extent, is something that every business will aim to achieve - this does not necessarily mean that they are lean organisations
Lean production is a systematic, whole-business approach to the reduction of waste. It is the bedrock of the business and determines every single choice made. Waste reduction is at the centre of every process and a culture of improvement is embedded.
Continuous Improvement (Kaizen)
Kaizen involves a business taking continuous steps to improve work processes and productive efficiency
Changes are small and ongoing rather than significant one-off’s and are constantly reviewed to ensure that the desired positive impact on productivity is achieved
Diagram: the Impact of continuous improvements on efficiency
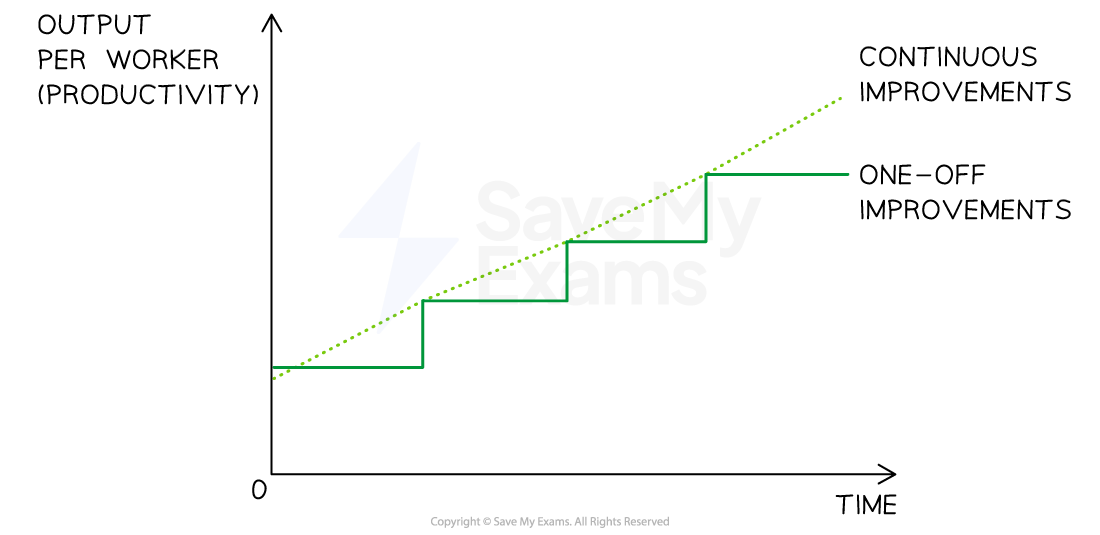
Elements of Kaizen commonly include
Total Quality Management
Team Working and quality circles
Zero defects in manufacturing
High levels of automation
High levels of cooperation between workers and management
Kaizen requires a long-term management commitment to change
Regular high quality training for all staff
Willingness to accept suggestions and delegate control to subordinate workers
Skills to implement and manage continual change
It is unlikely to cause workplace conflict
Workers do not face sudden significant change
Workers are wholly involved in - and contribute to - continuous improvement
Just-in-time (JIT)
Just in Time (JIT) stock management is a process in which raw materials are not stored onsite but ordered as required and delivered by suppliers 'just in time' for production
Careful coordination is required to ensure that raw materials and components are delivered by suppliers at the moment that they are to be used
Close relationships with suppliers need to be developed
Suppliers may need to be in close proximity
The Advantages and Disadvantages of Just in Time Stock Management
Advantages | Disadvantages |
---|---|
|
|
Cradle to Cradle Design
The traditional "cradle to grave" approach refers to the one-time use of a product
Products are designed with a linear life cycle that ends in disposal
This approach has led to an unsustainable increase in waste going to landfill and associated environmental concerns
The Cradle to Cradle (C2C) model aims to shift towards a circular economy
Resources are conserved and waste is minimised
It is focused on thoughtful design and responsible manufacturing practices
Key Principles of Cradle to Cradle Design and Manufacturing
Principle | Explanation | Example |
---|---|---|
Use responsible materials/components |
|
|
Design for Disassembly |
|
|
Use renewable energy |
|
|
Water stewardship |
|
|
Stakeholder responsibility |
|
|
Continuous improvement |
|
|
You've read 0 of your 5 free revision notes this week
Unlock more, it's free!
Did this page help you?