Stock Control (Edexcel A Level Business) : Revision Note
Interpretation of stock control diagrams
A stock control diagram illustrates the flow of stock (inventory) into and out of a business over time
Example stock control diagram
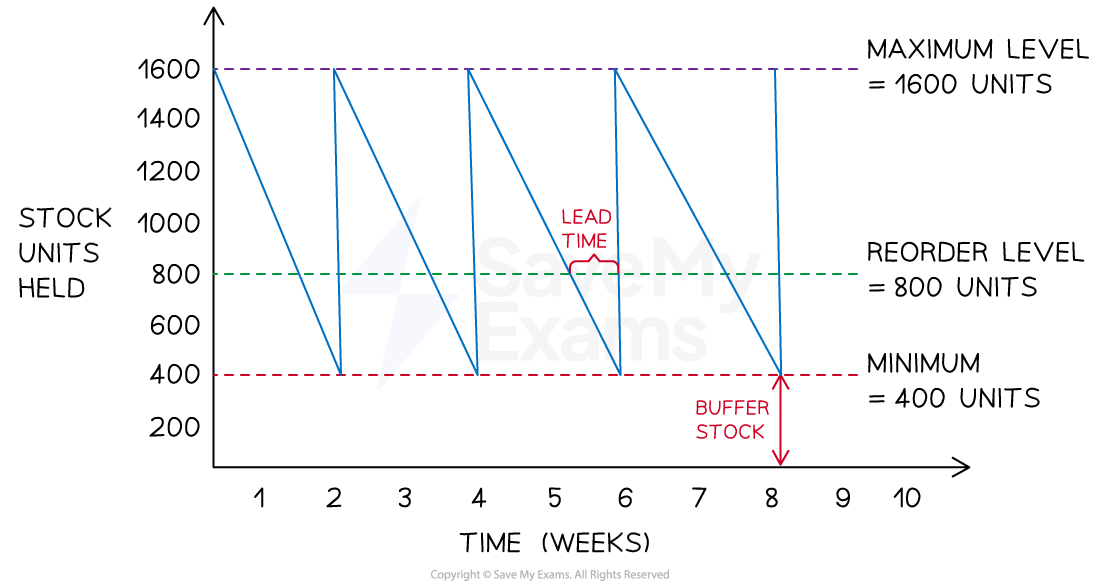
Diagram analysis
The maximum stock level is the maximum amount of stock a business is able to hold in normal circumstances (1600)
The reorder level is the level at which a business places a new order with its supplier (800)
The minimum stock level is also known as the buffer stock level and is the lowest level to which a business is willing to allow stock levels to fall (400)
The lead time is the length of time from the point of stock being ordered from the supplier to it being delivered (1 week)
The stock level line shows how stock levels change over the given time period
As stock is used up a downwards slope is plotted
When an order is delivered by a supplier the stock level line shoots upwards
Worked Example
The diagram below shows stock movements of kitchen shelving units sold by TamFix Ltd.
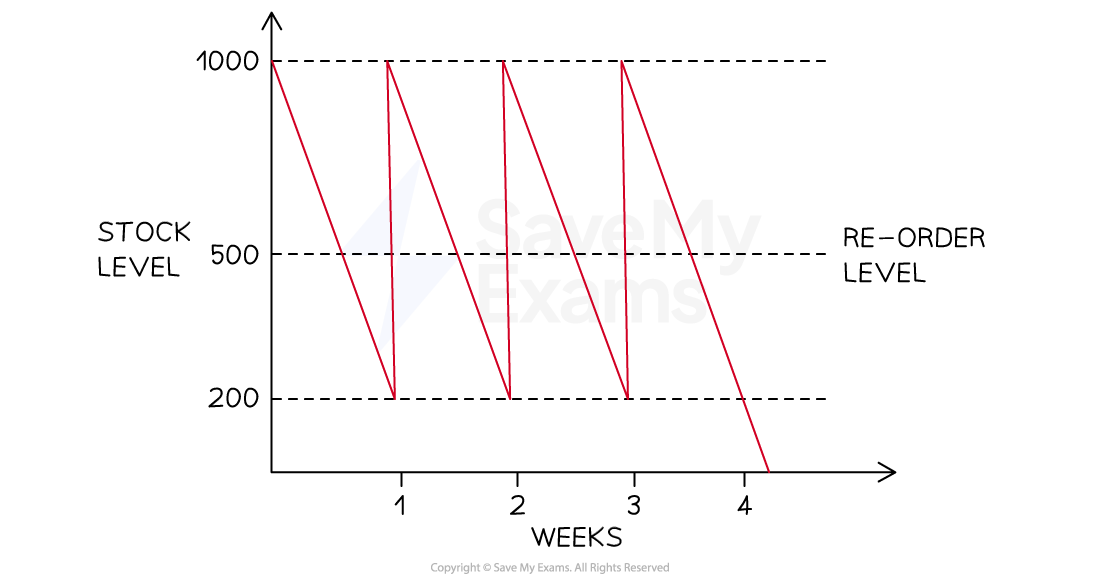
Identify the following points:
the minimum stock level
the re-order level
the re-order quantity
the lead time for kitchen shelving units (4)
Step 1 - Identify the minimum stock level
The minimum stock level is identified by the bottom-most dotted line - in this case it shows that the minimum stock level is 200 units (1)
Step 2 - Identify the reorder level
The reorder level is clearly identified on the diagram - in this case it shows that the reorder level is 500 units (1)
Step 3 - Identify the reorder quantity
The reorder quantity is the difference between the maximum stock level (shown by the topmost dotted line) and the minimum stock level
1000 units (maximum stock) - 200 units (minimum stock) = 800 units
The reorder quantity is therefore 800 units (1)
Step 4 - Identify the lead time for kitchen shelving units
The lead time is the difference in time between an order for stock being placed and its delivery. In this case, assuming a five-day working week, the lead time for shelving units is two days (1)
Buffer stock
Buffer stock is a quantity of goods/raw materials kept in case of stock shortages
This can provide a competitive edge over rivals unable to meet demand
This approach is commonly called ‘just in case’ stock control
The decision to keep buffer stocks is one that businesses have to weigh up very carefully
The decision will be influenced by the nature of the business and the product/service it provides
Advantages and disadvantages of holding buffer stock
Advantages | Disadvantages |
---|---|
|
|
Implications of poor stock control
Too much or too little stock: implications
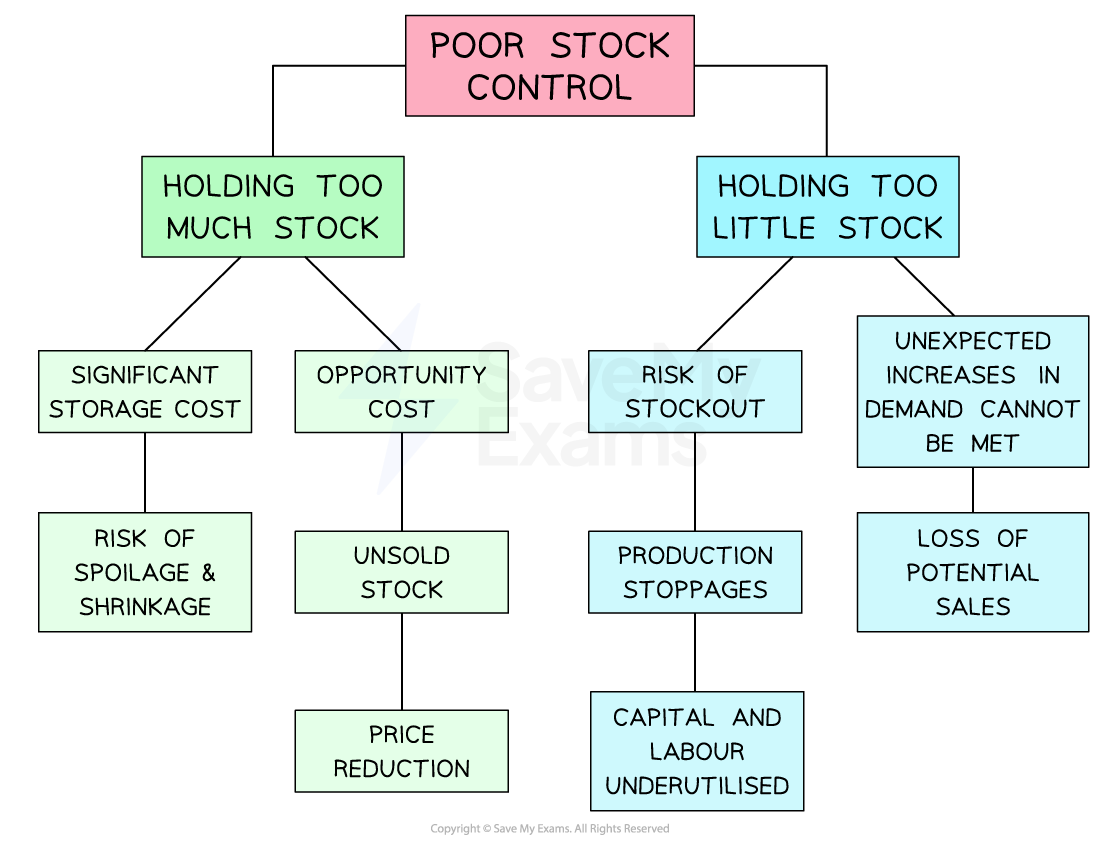
Problems may arise from holding too much stock
Storage costs (e.g. warehouse rental, security costs) will be higher than necessary
The risk of spoilage and stock shrinkage will be increased, leading to increased costs
Similarly, holding too little stock is risky
A business may run out of stock, resulting in production stoppages and higher unit costs related to underused capacity
A sudden increase in demand may not be capable of being met and this leads to a loss of potential sales revenue
Just in time (JIT) stock management
Just in Time (JIT) stock management is a process in which raw materials are not stored onsite
Stock is ordered as required, and delivered by suppliers 'just in time' for production
Careful coordination is needed to ensure that raw materials and components are delivered by suppliers at the moment that they are to be used
Advantages and disadvantages of just-in-time stock management
Advantages | Disadvantages |
---|---|
|
|
Waste minimisation
Waste in a business can occur for a number of reasons
Stock becomes obsolete unless used by a particular date
Perishable stock (food and medicines) that is not used before they deteriorate will need to be thrown away
Stock may be damaged as a result of poor storage conditions and may not be suitable for use in the production process
Allowing waste to go unchecked will increase the unit costs of production and reduce both efficiency and productivity
Businesses may take a range of steps to minimise waste
Ways to minimise waste
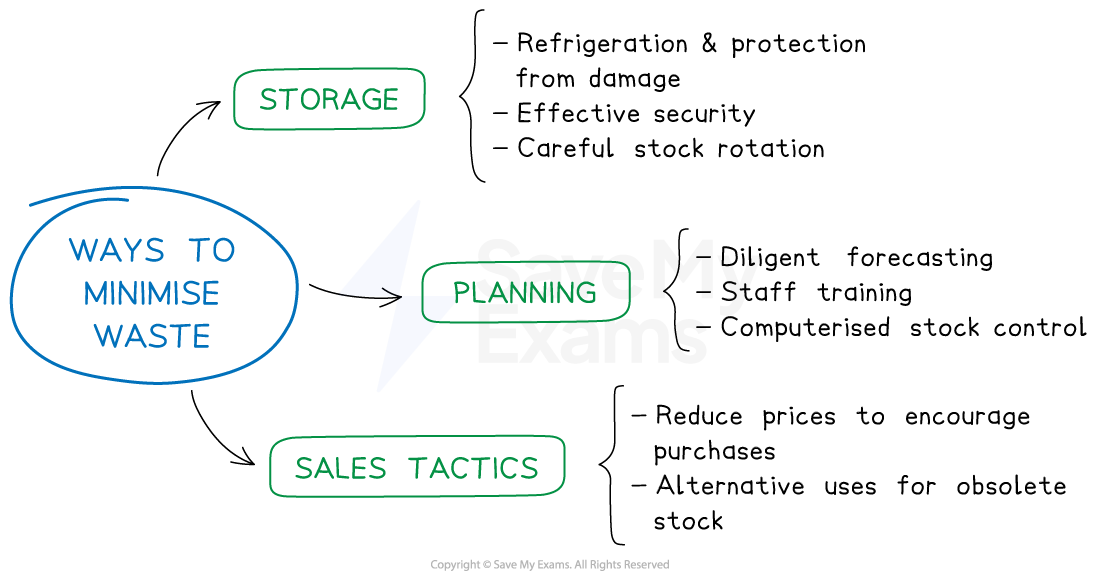
The minimisation of waste will depend upon the nature of the product
For perishable items, refrigeration and careful stock rotation can reduce waste
Staff training and computer inventory management systems may also reduce waste as fewer errors are likely to be made
Effective sales forecasting can help to reduce the amount of wasted stock
Competitive advantage from lean production
Lean production involves the minimisation of the resources used in production
Less time is required as the production process is organised in the most efficient way
Fewer materials are used as there is a focus on waste reduction
Less labour is used as lean production is typically capital intensive
The space required for production is reduced as a result of just in time stock management
A small number of trusted suppliers work closely with the business
The use of lean production is likely to lead to a competitive advantage
Lower unit costs are achieved due to minimal wastage, so prices may be lower than those offered by competitors
Better quality of output is likely as a result of supplier reliability and carefully managed production processes
You've read 0 of your 5 free revision notes this week
Sign up now. It’s free!
Did this page help you?